Oval conveyor systems made in Germany and China
Modular oval conveyor systems from KraussMaffei stand for fast and simple mold carrier changes, and therefore short set-up times. These are used in the automotive industry to manufacture foamed seats. KraussMaffei has been successfully producing these systems since 2012 at its location in Haiyan, China, specifically for the market in Asia. The scope of delivery primarily includes what is called dry side equipment, the actual oval conveyor with carriage and mold carriers, safety technology, a vacuum extractor and other peripheral components. “We were able to reduce the transport and service paths substantially through local production. That is something our customers in China and Southeast Asia value,” explains Christian Blatt, CEO of the KraussMaffei Group in China. Wet side equipment, mixing and metering systems and mixing heads are shipped from the headquarters in Munich, Germany. They stand for high precision and quality. They can reliably process up to six components.
Customized mold carriers
KraussMaffei has a diverse line of mold carriers for processing polyurethane. For example, a double-shuttle mold carrier is used especially for LFI applications, particularly for large components such as tractor roof modules, radiator grilles for trucks and interior paneling. An electric mold carrier is particularly suited for back-foaming of instrument panels. The WinCap mold carrier type was specially developed for window encapsulation, but it is also excellently suited for many other applications, such as solar panels.
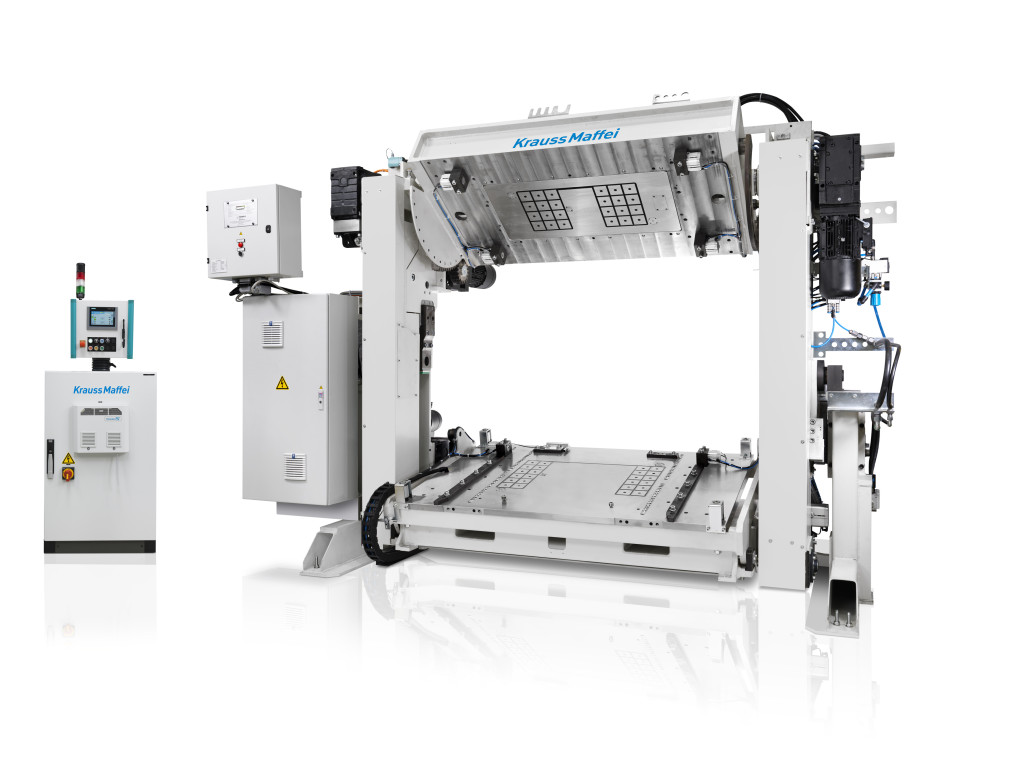
Wood lamination for the finest look and feel
Fine wood trim is an important element for underscoring the premium-quality look of a vehicle’s interior. Using the CCM (Clear Coat Molding) process developed by KraussMaffei, you can enhance these components with a scratch-resistant coating in a single work step. The automated process coats the wood very thinly with a clear two-component PU system. KraussMaffei’s patented cavity pressure regulation compensates for the volume fluctuations caused by the natural structure of the material. As a result, the cavity is always optimally filled.
Fiber-reinforced lightweight construction
Thanks to its wide-ranging expertise in the areas of injection molding and reaction process machinery, KraussMaffei is providing leading and innovative technologies and systems for processing thermoplastic and thermoset matrix systems from a single source. For PU China, the company is showing an exemplary assortment of components made from fiber composite materials that are not only solid and lightweight, but can be manufactured with the surface quality needed for product components with high visibility. Some examples are the LFI process (Long-Fiber Injection), which is particularly suited for large-format, contoured parts for trucks and agricultural machinery, and the HP-RTM process (high-pressure resin transfer molding), which enables manufacturing of carbon- or glass fiber-reinforced lightweight parts in a fully automated process that is suitable for series production.