Reduced maintenance costs thanks to SMS group torque retainer on converter tilt drive
The 100-ton AOD converter at the SěAH CSS stainless steel mill in Changwon, South Korea, was successfully re-commissioned in March 2018, after installation of an electro-hydraulic torque retainer from SMS group.
The purpose of the modernization was to minimize the destructive forces acting on the gears, bearings and converter car during gas injection.
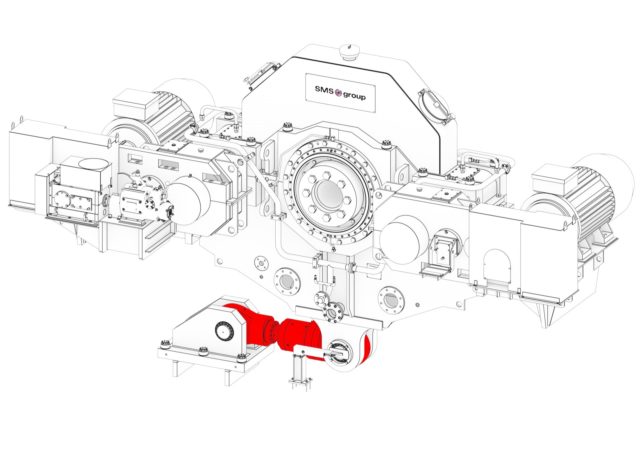
The scope of supply of SMS group (www.sms-group.com) comprised an electro-hydraulic torque retainer including electrical equipment and automation systems as well as the supervision of erection and commissioning.
The installation of the torque retainer was performed during a scheduled maintenance standstill and completed within ten days, including cold and hot commissioning. Hot commissioning even took place two days ahead of schedule under regular production conditions. The guaranteed values were fully reached. Thanks to the new electro-hydraulic torque retainer from SMS group, the dynamic loads on the entire converter equipment have been significantly reduced. This is the result of the successful cooperation between the teams from SěAH and SMS group.
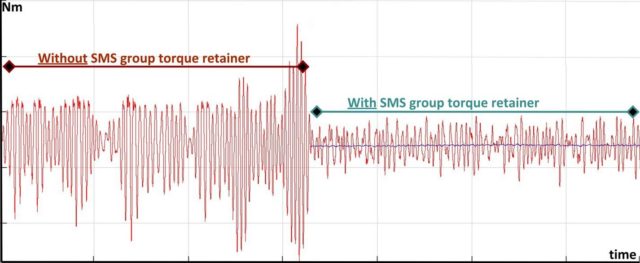
Seungheon Lee, General Manager Steelmaking Facility Team: “The new torque retainer from SMS group has significantly reduced the vibrations of the AOD converter. We experience the benefits of this modernization every day. Maintenance costs will be reduced significantly. We are very satisfied.”
SěAH Changwon Integrated Special Steel produces stainless steel, tool steel and carbon steel at a production volume of 1.2 million tons per year. The produced high-tech steel grades are used in a wide range of applications, for example in vehicles, machinery, aircrafts, nuclear power plants, shipbuilding and electronics.