Q2 FY22 Results: Strong performance
- Revenue of Rs. 57,893.59 Lakhs, YoY growth of 129.31%%
- EBITDA of Rs. 13,917.94 Lakhs, YoY growth of 205.36%
- PAT of Rs. 5,011.20 Lakhs, YoY growth of 2317.37%
- Quarterly EPS for Q2FY22 is Rs 15.68 per share
- Declared Second Interim dividend of Rs. 0.50 per share
Kolkata, October 11, 2021: Ramkrishna Forgings Limited (RKFL) is one of India’s leading forging companies has reported its financial results for the quarter and year ended September 30, 2021.
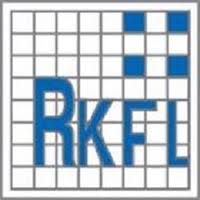
Standalone Financial Highlights
Particulars (in Rs. Lakhs) | Q2FY22 | Q2FY21 | YoY | Q1FY22 | QoQ | H1FY22 | H1FY21 | YoY |
Revenue# | 57,893.59 | 25,247.13 | 129.31% | 41,713.53 | 38.79% | 99,607.12 | 36,832.00 | 170.44% |
EBITDA# | 13,917.94 | 4,557.84 | 205.36% | 9,531.91 | 46.01% | 23,449.85 | 4,408.46 | 431.93% |
EBITDA (%) | 24.04% | 18.05% | 22.85% | 23.54% | 11.97% | |||
PAT | 5,011.20 | 207.30 | 2317.37% | 2,461.29 | 103.60% | 7,472.49 | -2,439.89 | |
PAT (%) | 8.66% | 0.82% | 5.90% | 7.50% | -6.62% |
# Excluding Other Income
Operational highlights for Q2FY22
- Received contracts worth ~Rs. 62,000 Lakhs from 8 contracts during the quarter from various geographies and business verticals
- Credit ratings upgrades:
- ICRA Limited : ICRA A (Stable)/ ICRA A1
- India Ratings & Research assigns IND A & IND A1; Stable Outlook
- Capacity Utilization
- Commencement of commercial production of fabrication facility and 2000 Ton warm Forging Press in September 2021 the total installed capacity reached 1,87,100 tonnes
- Overall capacity utilization was 78.81% (on enhanced capacity) for Q2FY22 as compared to 79.99% in Q1FY22
- Domestic Markets
- Achieved sales volume of 16,349 MT, a QoQ growth of 39.92% in Q2 FY22 as compared to 11,684 MT in Q1FY22 and a YoY growth of 69.95% as compared to Q2 FY21. Sales Volume grew by 115.31 % on YoY to 28,033 MT in H1FY22.
- Revenue growth of 51.58% in Q2 FY22 to Rs. 28,819.82 Lakhs as compared to Q1 FY22 and whereas growth on YoY basis was 115.87 % as compared to Q2 FY21
- Realization per MT improved by 8.35% to Rs. 176,280 per MT in Q2 FY22 as compared to Rs. 1,62,700 per MT in Q1 FY22 and by 27.02% from Rs. 138,778 per MT in Q2 FY21
- Exports Market
- Achieved sales volume of 11,930 MT, a QoQ growth of 16.72 % in Q2 FY22 as compared to 10,221 MT in Q1 FY22 and a YoY growth of 101.22% as compared to Q2 FY21
- Revenue growth of 28.88% in Q2 FY22 to Rs. 28,673.78 Lakhs as compared to Q1 FY22 and whereas growth on YoY basis was 151.73% as compared to Q2 FY21
- Realization per MT improved by 6.52% to Rs. 2,27,434 per MT in Q2 FY22 as compared to Rs. 2,13,507 per MT in Q1 FY22 and by 18.38 % from Rs. 192,120 per MT in Q2 FY21
- North America contributed 73.33% in Q2 FY22 as compared to 70.80% in Q1 FY22 and 70.00% in Q2 FY21 whereas Europe contributed 25.80% in Q2 FY22 as compared to 28.30% in Q1 FY22 and 28.76% in Q2 FY21. Other Markets contributed 0.90% in Q2 FY22 as compared to 0.90% in Q1 FY22 and 1.25% in Q2 FY21
Commenting on the results Mr. Mahabir Prasad Jalan, Chairman, Ramkrishna Forgings Limited said:
“The Company has achieved a turnover of Rs 57,893.59 Lakhs in Q2FY22 in comparison to Rs 25,247.13 Lakhs in Q2FY21 registering an increase of 129.31% YoY and Rs 99,607.12 Lakhs in H1FY22 in comparison to Rs 36,832.00 Lakhs in H1FY21 registering an increase of 170.44% YoY. The Company has achieved an Export turnover of Rs 28,673.78 Lakhs in Q2FY22 comparison to Rs 11,390.78 Lakhs in Q2FY21, registering a growth of 151.73% and an Export turnover of Rs 50,698.79 Lakhs in H1FY22 comparison to Rs 18,006.05 Lakhs in H1FY21, registering a growth of 181.57%. The EBDITA (excl. other income) is also increased to Rs 13,917.94 Lakhs in Q2FY22 in comparison to Rs 4,557.84 Lakhs in Q2FY21 and Rs. 23,449.85 Lakhs in H1FY22 as compared to Rs. 4,408.46 Lakhs in H1FY21. The PAT has also increased to Rs 5,011.20 Lakhs in Q2FY22 from Rs 207.30 Lakhs in Q2FY21 and to Rs. 7,472.49 Lakhs in H1FY22 from Rs. -2,439.89 Lakhs in H1FY21.
With all the capacity expansions in place taking our overall capacity to 1,87,100 tons per annum, we expect to increase our presence in Indian as well as exports markets and deliver new products which might help us to improve our operating leverage and boost our margins
With the help of our research and development and various initiatives we can offer improved and premium products to our customer. Our strategy of diversifying our presence in both auto and non- auto segment along with strengthening presence in exports market has been bearing fruits with recent order wins.”
Adding further on the results Mr. Naresh Jalan, Managing Director said:
“Our company has reported strong results across various business parameters. During the quarter we managed to win contracts across all business segments and entered new geographies thus gaining further grounds on our sector as well as geographic diversification strategy.
We have marked our presence in EV segment by winning our first EV contract which a testimony of our technological prowess.
Our contract wins in oil & gas segment strengthens our penetration into this sector and is in line with the strategy to diversify its portfolio across sectors and geographies.
Looking ahead into second half of FY22, we expect the overall growth to continue supported by recovery in the domestic automotive markets and sustained improvement in exports.
Potential impact on OEM production schedule due to semiconductors supply crunch, increase of input costs and freight cost are factors to keep track of in the coming months.
Looking at the visibility of the business, we hope the recent recovery in Commercial Vehicle segment continues for the balance period of the year which will enable us to post a strong growth foundation for coming years.”
About Ramkrishna Forgings Limited
Ramkrishna Forgings was incorporated in 1981 with the objective to manufacture forged products. The Annualized installed capacity after commissioning of Hollow Spindle Line, a new 7000 Ton Press Line, a 2000 Ton warm/hot Forming Press and a fabrication facility is 187,100 MT. headquartered at Kolkata, the company has state-of-the-art manufacturing facilities at Jamshedpur along with offices at Detroit in USA, Toluca and Monterrey in Mexico, Istanbul in Turkey having warehousing facilities at Hagerstown, Louisville, Detroit in USA, Toluca, Monterrey in Mexico and Westerloo in Belgium. Over the years, the company increased its forging and die making capacities and added machining and heat treatment facilities, including isothermal annealing, which enabled it to undertake manufacturing of components for OEMs and Tier 1 companies, The Company is certified in terms of TS 16949, OSHAS 18001 and ISO 14001 and is a manufacturer & supplier of closed die forgings of carbon and alloy steel, micro alloy steel and stainless steel forgings which can be supplied in As Forged + Heat Treated + Machined and Fully assembled condition as per the customer’s requirement. The Company is suppliers to various sectors like Automotive, Railways, Farm Equipment, Bearings, Oil & Gas, Power and Construction, Earth Moving & Mining, both in India & overseas markets. The Company is a critical safety item supplier for undercarriage, Bogie & Shell parts for railway passenger coaches and locomotives. It is a preferred supplier to OEMs like TATA Motors, Ashok Leyland, VE Commercial and Daimler in India and to Volvo, Mack Trucks, Iveco, DAF, Scania, MAN, UD Trucks and Ford otosan in the overseas markets. It supplies globally to Tier 1 axle manufacturers like Dana, Meritor and American Axles.